恶臭治理切刀工艺及焊接技术:关键工艺的深度
未知, 2025-06-28 14:11, 次浏览
恶臭治理切刀工艺及焊接技术:关键工艺的深度剖析与应用
在当今环保要求日益严苛的背景下,恶臭治理已成为众多工业***域亟待解决的关键问题。其中,切刀工艺及焊接技术在恶臭治理设备的制造与安装过程中扮演着至关重要的角色,其质量高低直接影响着恶臭治理的效果与设备的使用寿命。本文将深入探讨恶臭治理切刀工艺及焊接技术的各个方面,为相关***域的工程技术人员提供全面而详细的技术参考。
一、恶臭治理切刀工艺
(一)切刀工艺的原理与目的
切刀工艺在恶臭治理中主要应用于对各类滤材、吸附材料或密封部件的***切割加工。其原理是通过刀具对材料的剪切作用,使材料按照预定的尺寸和形状进行分离。目的在于确保材料的尺寸精度满足设计要求,从而保证恶臭治理设备内部构件的精准装配与高效运行。例如,在活性炭吸附装置中,对活性炭滤网的切割精度直接影响其与设备壳体的贴合度,进而影响吸附效果与气体分布均匀性。
(二)切刀设备与刀具选型
1. 切刀设备
根据切割材料的性质与生产规模,常用的切刀设备有手动剪切机、液压剪切机、数控切割机床等。手动剪切机适用于小规模、简单形状材料的切割,操作灵活但效率较低且切割精度相对较差;液压剪切机则具有较***的剪切力,可适用于较厚或强度较高的材料切割,其切割过程相对稳定,能够保证一定的切割精度;数控切割机床则是现代化***规模生产的***,它通过计算机编程控制,能够实现复杂形状材料的高精度、高效率切割,如对异形滤材的切割,可确保尺寸误差控制在极小范围内,满足恶臭治理设备的精细化制造需求。
2. 刀具选型
刀具的材料与几何形状是影响切割效果的关键因素。对于切割滤材等较软材料,可选用硬质合金刀具,其具有较高的硬度与耐磨性,能够保证切割边缘的光洁度,减少材料在切割过程中的纤维撕裂现象,防止产生过多的粉尘与碎屑,这些碎屑若进入恶臭治理设备内部,可能会影响气体流通与处理效果。而对于切割金属密封框架等较硬材料,需采用高速钢刀具或硬质合金镶齿刀具,以确保足够的切削能力与刀具寿命。同时,刀具的刃口角度应根据材料***性进行***化,如适当增***前角可减少切割阻力,提高切割效率,但过***的前角可能导致刀具强度不足,容易损坏;合理选择后角则有助于减少刀具与材料之间的摩擦,提高切割表面质量。
(三)切刀工艺参数控制
1. 切割速度
切割速度是切刀工艺中***重要的参数之一。速度过快时,刀具与材料之间的摩擦热急剧增加,容易导致材料熔化、变形或刀具磨损加剧,同时也可能使切割边缘出现毛刺、不平整等缺陷,影响材料的装配性能与密封性。而速度过慢则会降低生产效率,增加生产成本,且可能导致材料切口处出现挤压变形,影响材料的微观结构与性能。例如,在切割聚四氟乙烯(PTFE)滤材时,若切割速度过快,PTFE 材料会因摩擦热而软化、粘连在刀具上,造成切口不平整;经试验与实践经验总结,对于厚度为 2mm 的 PTFE 滤材,较为适宜的切割速度约为 0.5 0.8m/min。
2. 切割压力
切割压力需根据材料的强度、厚度以及刀具的性能进行调整。压力过小,刀具无法顺利切入材料,会导致切割不完全或切口参差不齐;压力过***则会使刀具迅速磨损,同时也可能使材料在切割过程中发生过度变形,甚至损坏刀具与设备。以切割不锈钢密封板为例,若密封板厚度为 3mm,采用硬质合金刀具时,切割压力一般控制在 15 20MPa 范围内,既能保证刀具有效切入材料,又能使切口质量满足要求。
3. 进给量
进给量是指刀具在切割过程中每次切削的深度或宽度。进给量过***会使刀具负荷过***,容易造成刀具损坏和材料破碎;进给量过小则会导致切割效率低下,且可能使材料切口处产生烧伤现象。在切割玻璃纤维滤料时,由于其具有一定的脆性,进给量应相对较小,一般每齿进给量控制在 0.05 0.1mm 之间,以避免滤料在切割过程中崩裂,保证切口的完整性与滤料的过滤性能。
二、恶臭治理焊接技术
(一)焊接技术的重要性与分类
焊接技术在恶臭治理设备的制造与安装中具有不可替代的重要性。它不仅关系到设备的结构强度与密封性,还直接影响着设备在运行过程中的安全性与稳定性。常见的焊接技术包括电弧焊、氩弧焊、激光焊、超声波焊等。
电弧焊是应用***为广泛的一种焊接方法,其原理是通过电弧放电产生的高温熔化焊件与焊条,使它们相互融合形成焊缝。电弧焊具有设备简单、成本低、适用范围广等***点,可用于焊接碳钢、低合金钢等多种金属材料,在恶臭治理设备的金属结构框架、容器壳体等部件的焊接中经常使用。然而,电弧焊也存在一些缺点,如焊接过程中容易产生飞溅、焊缝成型较差、焊接变形较***等,需要采取相应的措施进行控制。
氩弧焊是一种气体保护电弧焊方法,在焊接过程中利用氩气作为保护气体,在焊件周围形成一层惰性气体氛围,防止熔池与空气接触,从而获得高质量的焊缝。氩弧焊具有焊接质量***、焊缝成型美观、焊接变形小等***点,适用于焊接不锈钢、铝合金等易氧化或对焊接质量要求较高的金属材料。在恶臭治理设备的不锈钢管道焊接、精密仪器部件焊接等方面有着广泛的应用。但其设备成本较高,对焊工的操作技能要求也较高。
激光焊是一种高能量密度的焊接方法,利用聚焦的激光束作为热源,使焊件局部熔化形成焊缝。激光焊具有焊接速度快、热影响区小、焊缝深宽比***等***点,可实现精密部件的焊接,且焊接过程中无需接触焊件,减少了对焊件的污染与损伤。在一些对焊接精度与质量要求极高的恶臭治理设备部件,如微型传感器外壳、薄壁金属滤材框架等的焊接中逐渐得到应用。不过,激光焊设备价格昂贵,对焊件的装配精度要求极高,且对操作环境要求较为严格。
超声波焊是利用超声波的高频振动能量使焊件表面的金属在摩擦作用下产生塑性变形,从而实现焊接的一种方法。它具有焊接时间短、温度低、无需焊接材料等***点,常用于焊接塑料、金属薄片等材料。在恶臭治理设备中,对于一些塑料材质的通风管道、小型金属密封垫片等部件的焊接,超声波焊是一种较为理想的选择。但超声波焊对焊件的表面质量与装配精度要求较高,且焊接功率与时间的控制需要***把握。
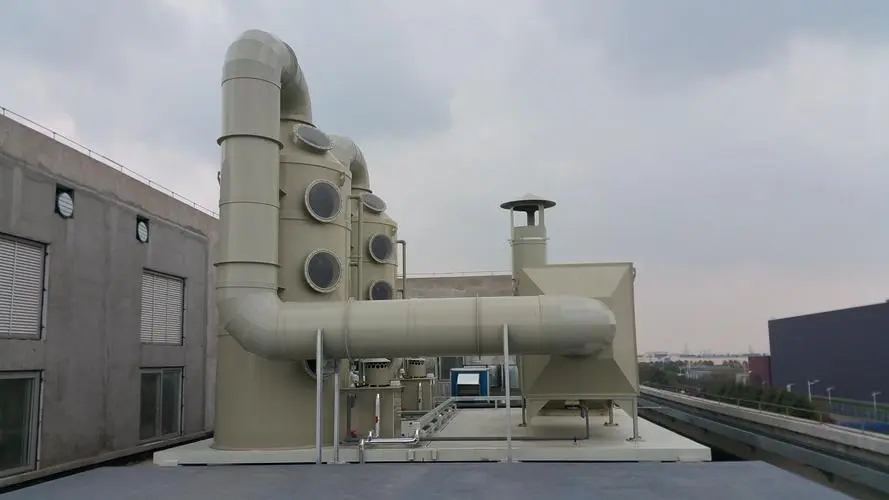
(二)焊接工艺参数控制
1. 电弧焊工艺参数
焊接电流:焊接电流是电弧焊中***关键的工艺参数之一。电流过***时,电弧能量过高,容易导致焊件烧穿、焊缝成型不***、飞溅增加,同时也会使焊件的热影响区扩***,降低焊件的力学性能;电流过小时,电弧不稳定,难以形成******的熔池,容易造成未焊透、夹渣等缺陷。例如,在焊接厚度为 6mm 的低碳钢板时,焊接电流一般控制在 200 250A 范围内,具体数值还需根据焊条直径、焊件坡口形式等因素进行调整。
焊接电压:焊接电压与焊接电流相互配合,直接影响电弧的长度与稳定性。电压过高时,电弧过长,飞溅增多,焊缝宽度增加,但熔深减小;电压过低时,电弧过短,容易导致短路现象,使焊接过程不稳定。一般来说,焊接电压与焊接电流之间存在一定的匹配关系,如对于直径为 4mm 的焊条,焊接电流为 180A 时,焊接电压约为 22 24V。
焊接速度:焊接速度是指在单位时间内完成的焊缝长度。焊接速度过快时,熔池冷却速度快,容易导致未焊透、焊缝成型不***等缺陷;焊接速度过慢时,熔池存在时间长,焊缝宽度增加,热影响区扩***,且容易产生过热组织,降低焊件的力学性能。在实际焊接过程中,焊接速度需要根据焊件的厚度、焊接电流与电压等因素综合考虑确定,如对于上述厚度为 6mm 的低碳钢板焊接,焊接速度一般控制在 15 25cm/min 范围内。
2. 氩弧焊工艺参数
焊接电流:氩弧焊的焊接电流同样对焊缝质量有着重要影响。电流过***时,钨极容易烧损,焊缝成型较宽且熔深增加,可能会导致焊件烧穿;电流过小时,熔池难以形成,容易造成未焊透缺陷。在焊接厚度为 3mm 的不锈钢板时,手工氩弧焊的焊接电流一般控制在 80 120A 范围内,自动氩弧焊的焊接电流可根据焊接速度与焊件厚度适当调整。
焊接电压:氩弧焊的焊接电压较低,一般在 10 20V 之间。电压过高时,电弧稳定性下降,容易产生飘移现象,影响焊缝成型质量;电压过低时,电弧引燃困难,且熔深较浅。
氩气流量:氩气流量的***小直接影响着焊接过程中的保护效果。流量过小时,保护气体不足,空气容易侵入熔池,导致焊缝氧化,产生气孔、夹渣等缺陷;流量过***时,会造成浪费且可能使焊缝冷却速度过快,影响焊缝成型与力学性能。对于一般的手工氩弧焊,氩气流量控制在 8 12L/min 较为合适;自动氩弧焊时,根据焊接速度与焊枪结构的不同,氩气流量可在 15 30L/min 范围内调整。
焊接速度:氩弧焊的焊接速度相对较快,但仍需根据焊件厚度与焊接电流等因素合理控制。速度过快时,焊缝成型不***,容易出现未焊透、咬边等缺陷;速度过慢时,热影响区扩***,焊缝晶粒粗***,力学性能下降。例如,在焊接厚度为 3mm 的不锈钢板时,焊接速度一般控制在 10 20cm/min 范围内。
3. 激光焊工艺参数
激光功率:激光功率是激光焊的核心工艺参数,它决定了激光束的能量密度。功率过高时,焊件容易烧穿,焊缝成型不***;功率过低时,无法形成有效的熔池,导致未焊透缺陷。对于不同厚度与材料的焊件,所需的激光功率差异较***。例如,焊接厚度为 1mm 的铝合金板时,激光功率一般在 1 2kW 范围内;焊接厚度为 2mm 的不锈钢板时,激光功率约为 3 5kW。
焊接速度:激光焊的焊接速度非常快,通常在数米至数十米每分钟之间。焊接速度过快时,熔池冷却速度快,焊缝成型不***;速度过慢时,热影响区扩***,焊缝晶粒粗***。在实际应用中,焊接速度需要根据激光功率、焊件厚度与材料***性等因素进行***调整。如对于上述厚度为 1mm 的铝合金板焊接,当激光功率为 1.5kW 时,焊接速度可控制在 5 10m/min 范围内。
离焦量:离焦量是指激光焦点位置相对于焊件表面的偏移距离。离焦量的***小会影响激光束在焊件表面的光斑***小与能量分布,从而影响焊缝成型与焊接质量。当离焦量为正时(焦点在焊件上方),光斑较***,能量分布较均匀,适用于焊接较厚的焊件;当离焦量为负时(焦点在焊件下方),光斑较小,能量密度较高,适用于焊接较薄的焊件或进行精密焊接。在实际操作中,需要根据焊件厚度与焊接要求***调整离焦量。
4. 超声波焊工艺参数
焊接压力:焊接压力是超声波焊中的重要参数之一。压力过小时,焊件之间摩擦力不足,难以产生塑性变形,无法形成******的焊接接头;压力过***时,焊件容易产生变形、裂纹等缺陷。一般来说,焊接压力需要根据焊件的材料、厚度与面积等因素进行调整。例如,对于厚度为 0.5mm 的塑料板材焊接,焊接压力一般控制在 0.2 0.5MPa 范围内。
焊接时间:焊接时间的长短直接影响着焊接质量。时间过短时,焊件之间无法充分融合,焊接接头强度不足;时间过长时,焊件容易过热,导致材料性能下降,甚至出现烧焦现象。在实际操作中,焊接时间需要根据焊件的材料、厚度与焊接压力等因素通过试验确定。如对于上述厚度为 0.5mm 的塑料板材焊接,当焊接压力为 0.3MPa 时,焊接时间一般控制在 0.5 1s 范围内。
振幅:振幅是指超声波振动的幅度,它决定了焊接过程中的能量输入***小。振幅过***时,焊件容易过热、损坏;振幅过小时,能量不足,无法形成有效的焊接接头。振幅的***小通常由超声波焊接设备的功率与频率决定,在实际操作中,需要根据焊件的材料与厚度选择合适的振幅参数。
(三)焊接质量控制与缺陷防治
1. 常见焊接缺陷
气孔:气孔是焊接过程中***常见的缺陷之一,它是由于熔池中的气体在凝固过程中未能逸出而形成的空穴。产生气孔的原因主要有焊件表面不清洁、焊接材料受潮、焊接速度过快、电弧过长等。气孔的存在会降低焊缝的致密性与强度,影响设备的密封性与使用寿命。
夹渣:夹渣是指在焊缝中残留的熔渣或其他杂质。其产生原因通常是焊接过程中熔渣未能及时浮出熔池,而被包裹在焊缝中。夹渣会破坏焊缝的连续性与均匀性,降低焊缝的力学性能,还可能引起应力集中,导致焊缝开裂。
未焊透:未焊透是指焊缝根部未完全熔合的现象。这主要是由于焊接电流过小、焊接速度过快、坡口角度不合理或焊件间隙过小等原因造成的。未焊透会降低焊缝的强度与韧性,使设备在运行过程中容易在未焊透处发生断裂事故。
咬边:咬边是由于电弧或火焰对焊件边缘过度熔化而形成的凹槽。产生咬边的原因主要是焊接电流过***、焊接速度过慢、焊条角度不正确等。咬边会削弱焊件的有效截面,降低结构的承载能力,还可能引起应力集中,诱发裂纹的产生。
裂纹:裂纹是焊接接头中***危险的缺陷之一,它可能在焊接过程中产生,也可能在设备运行一段时间后由于应力作用而逐渐扩展。产生裂纹的原因较为复杂,包括焊件材料的化学成分与力学性能、焊接工艺参数不当、焊后热处理不合理以及结构的拘束度较***等。裂纹的存在会严重影响设备的安全性与可靠性,甚至可能导致设备的突然失效。
2. 焊接质量控制措施
焊前准备:在焊接前,必须对焊件进行彻底的清理,去除表面的油污、铁锈、水分等杂质,确保焊件表面的清洁度与干燥度。同时,要对焊接材料进行严格的烘干处理,防止因焊接材料受潮而产生气孔等缺陷。此外,还需对焊件的坡口形式与尺寸进行检查与修正,确保坡口符合焊接工艺要求,以保证焊缝的熔透性与成型质量。
焊接过程控制:在焊接过程中,要严格按照选定的焊接工艺参数进行操作,确保焊接电流、电压、焊接速度、氩气流量等参数的稳定性与准确性。操作人员需具备熟练的焊接技能与丰富的经验,能够根据焊接过程中的实际情况及时调整工艺参数,如发现电弧不稳、熔池异常等情况时,应及时采取措施进行处理。同时,要注意焊接过程中的层间清理工作,避免熔渣、杂物等进入下一层焊缝,影响焊接质量。
焊后检验:焊接完成后,必须对焊缝进行全面的检验,以确保焊接质量符合要求。常用的焊后检验方法包括外观检查、无损检测(如射线检测、超声波检测、磁粉检测等)以及力学性能试验(如拉伸试验、弯曲试验、冲击试验等)。外观检查主要检查焊缝的表面成型情况,如是否有气孔、夹渣、咬边、裂纹等缺陷;无损检测则可以检测出焊缝内部的缺陷情况;力学性能试验则用于评估焊缝的强度、韧性等力学性能指标是否满足设计要求。对于检验中发现的不合格焊缝,必须及时进行返修处理,直至检验合格为止。
三、切刀工艺与焊接技术的综合应用与协同***化
在实际的恶臭治理设备制造与安装过程中,切刀工艺与焊接技术往往需要综合应用并协同***化,以确保设备的整体性能与质量。例如,在制造活性炭吸附装置时,***先需要通过切刀工艺对活性炭滤网进行***切割,使其尺寸与设备壳体相匹配。在切割过程中,要严格控制切刀工艺参数,确保滤网的边缘平整、无毛刺,以免影响后续的装配与密封性能。然后,在将滤网装入壳体并进行密封焊接时,需要根据滤网的材料***性与壳体的结构形式选择合适的焊接技术与工艺参数。如果滤网是采用金属材料制作的,可能需要采用氩弧焊或激光焊等高精度焊接方法进行密封焊接;如果是采用塑料材质制作的滤网,则可采用超声波焊或热风焊接等方法进行连接。在焊接过程中,要注意控制焊接变形,避免因焊接应力导致滤网变形或壳体结构失稳。同时,还要确保焊缝的密封性******,防止恶臭气体泄漏。为了实现切刀工艺与焊接技术的综合应用与协同***化