恶臭治理中全自动焊接技术与工艺控制的关键作
未知, 2025-06-13 09:40, 次浏览
恶臭治理中全自动焊接技术与工艺控制的关键作用
本文深入探讨了在恶臭治理***域,全自动焊接技术的应用以及工艺控制的重要性。详细介绍了全自动焊接技术在恶臭治理设备制造中的***势,包括提高焊接质量、稳定性和生产效率等方面。同时,阐述了工艺控制在确保焊接过程精准性、可靠性以及***终设备性能方面的关键作用。通过实际案例分析,展示了合理运用全自动焊接技术与严格工艺控制对恶臭治理项目成功实施的积极影响,为相关***域的工程实践提供了有价值的参考。
一、引言
随着环保要求的日益严格,恶臭治理已成为众多行业面临的重要课题。在恶臭治理系统中,设备的质量和性能至关重要,而焊接作为设备制造的关键环节之一,直接影响着设备的整体运行效果和使用寿命。传统的手工焊接方式存在诸多局限性,如焊接质量不稳定、效率低下等。全自动焊接技术的出现为恶臭治理设备的制造带来了新的机遇,而与之相辅相成的工艺控制则是确保焊接质量和设备性能的核心保障。
二、恶臭治理设备对焊接的要求
(一)密封性要求
恶臭治理设备通常需要处理各种有害气体,对密封性要求极高。任何微小的焊接缝隙都可能导致气体泄漏,不仅影响治理效果,还可能对环境和人员安全造成威胁。例如,在废气处理塔的焊接中,若焊接不严密,废气中的恶臭成分可能会逸出,降低处理效率并污染周边环境。
(二)耐腐蚀性要求
许多恶臭物质具有腐蚀性,因此设备材料和焊接部位需要具备******的耐腐蚀性。焊接过程必须保证焊缝的化学成分和金相组织均匀,避免因焊接缺陷导致局部腐蚀加剧,缩短设备使用寿命。比如在处理含酸性恶臭气体的设备中,焊缝若存在气孔、夹渣等缺陷,容易成为腐蚀的起始点,加速设备的腐蚀破坏。
(三)强度和稳定性要求
恶臭治理设备在运行过程中可能会承受一定的压力、温度变化以及机械振动等负荷。焊接部位必须具有足够的强度和稳定性,以确保设备在长期运行中不会发生变形、破裂等故障。例如,在***型恶臭处理风机的焊接结构中,焊缝的强度直接关系到风机的安全运行和性能稳定性。
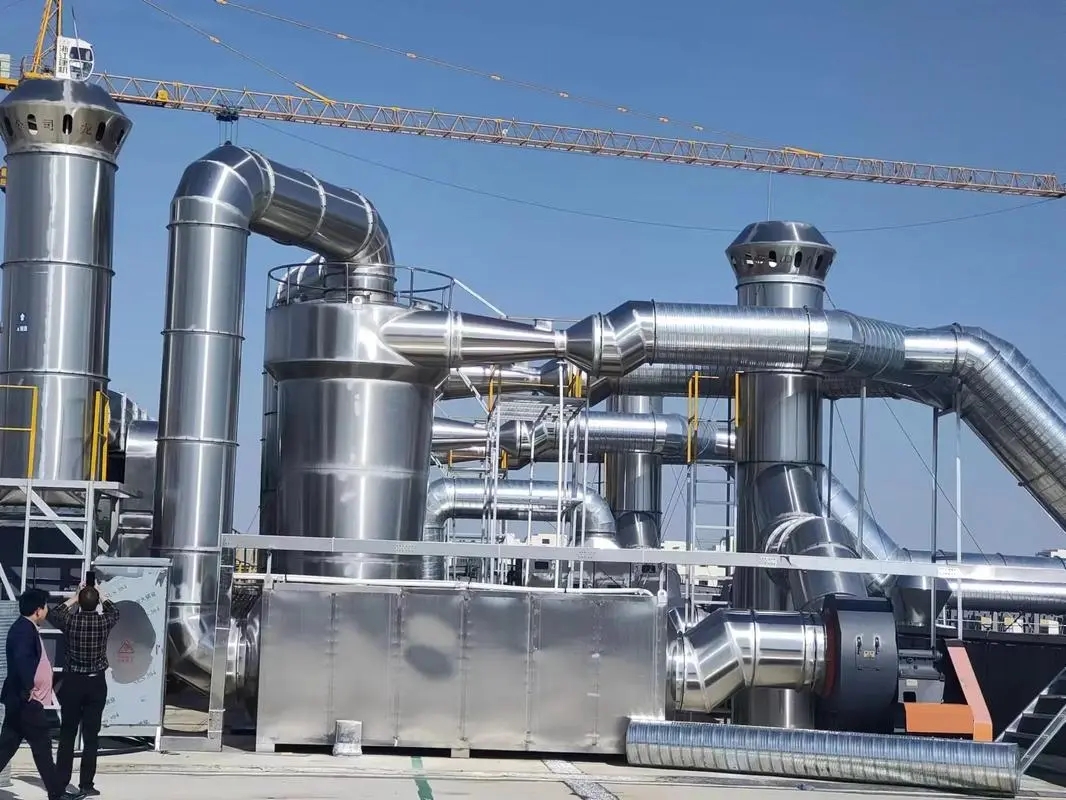
三、全自动焊接技术在恶臭治理中的应用***势
(一)提高焊接质量
1. ***的焊接参数控制
全自动焊接设备能够***设定和控制焊接电流、电压、焊接速度、送丝速度等参数。与传统手工焊接相比,避免了人为因素导致的参数波动,保证了每个焊缝的焊接质量一致性。例如,在管道焊接中,全自动焊接系统可以根据管道材质和厚度自动调整***焊接参数,确保焊缝成型美观、均匀,无气孔、夹渣等缺陷。
2. 先进的焊接工艺
全自动焊接技术可以采用多种先进的焊接工艺,如气体保护焊、埋弧焊等。这些工艺能够有效保护焊接熔池,减少杂质和气体的侵入,提高焊缝的纯净度和质量。例如,氩弧焊在焊接过程中使用惰性气体氩气作为保护气体,能够在高温下防止焊缝氧化,***别适用于对耐腐蚀性要求较高的恶臭治理设备焊接。
(二)提升生产效率
1. 高焊接速度
全自动焊接设备的焊接速度通常比手工焊接快得多。它可以持续稳定地进行焊接作业,无需频繁休息和调整,******缩短了设备制造周期。例如,在批量生产恶臭治理用的金属滤筒时,全自动焊接设备能够快速完成滤筒的卷圆焊接,提高了生产效率,满足***规模生产需求。
2. 自动化流程
全自动焊接系统可以实现自动化的焊接流程,包括工件的装夹、定位、焊接以及焊后处理等环节。减少了人工操作的繁琐步骤,降低了劳动强度,同时提高了生产过程的可控性和稳定性。例如,通过机器人自动化焊接工作站,可以一次性完成多个部件的焊接,实现了高效的生产作业。
(三)降低人为误差
手工焊接容易受到焊工技术水平、疲劳程度、情绪等因素的影响,导致焊接质量参差不齐。而全自动焊接技术依靠预设的程序和***的控制系统,能够始终按照标准要求进行焊接操作,有效避免了人为误差。这不仅保证了焊接质量的稳定性,还提高了产品的合格率,减少了因焊接缺陷导致的返工和维修成本。
四、工艺控制在全自动焊接中的重要性
(一)焊接参数的***化与匹配
1. 材料***性与参数选择
不同的恶臭治理设备材料具有不同的焊接***性,如碳钢、不锈钢、合金钢等。工艺控制需要根据材料的化学成分、力学性能和焊接性,***化选择合适的焊接参数。例如,对于不锈钢材料,需要考虑其热敏感性和晶间腐蚀倾向,选择合适的焊接电流和冷却速度,以防止焊缝出现晶间腐蚀问题。
2. 厚度与结构因素
设备的厚度和结构形式也会影响焊接参数的选择。较厚的板材需要更***的焊接电流和更长的焊接时间,但同时也要注意避免过热导致变形和质量问题。对于复杂的结构,如管板焊接、角接焊缝等,需要根据实际情况调整焊接角度、顺序和参数,确保焊缝的质量和强度。例如,在管板焊接中,要根据管径和板厚合理调整焊接电流和氩气流量,以保证焊缝的根部融合和表面成型。
(二)焊前准备与预处理
1. 材料表面处理
工艺控制要求在焊接前对材料表面进行严格的处理,去除油污、铁锈、氧化膜等杂质。这些杂质会影响焊缝的成型和质量,甚至导致焊接缺陷。例如,采用喷砂、抛丸等方法对金属表面进行处理,使其达到一定的清洁度和粗糙度,有利于提高焊缝的附着力和结合强度。
2. 工件装配与定位
准确的工件装配和定位是保证焊接质量的前提。工艺控制需要规定工件的装配间隙、错边量等参数,并通过专用的夹具和定位装置进行固定。例如,在筒体环缝焊接时,要确保筒体的椭圆度和纵环缝的错边量在允许范围内,以保证焊缝的均匀性和设备的圆度要求。
(三)焊接过程监控与质量控制
1. 实时监测
在全自动焊接过程中,工艺控制需要对焊接参数、焊缝成型等进行实时监测。通过安装传感器和监控系统,可以及时检测到焊接过程中的异常情况,如焊接电流波动、电压异常、送丝不畅等,并及时发出警报和调整指令。例如,采用激光位移传感器监测焊缝的余高和宽度,确保焊缝尺寸符合要求。
2. 质量检测与评估
焊接完成后,需要对焊缝进行全面的质量检测和评估。常用的检测方法包括外观检查、无损检测(如超声波检测、射线检测、磁粉检测等)。工艺控制要根据设备的重要性和使用要求,确定合适的检测方法和验收标准。例如,对于压力容器类的恶臭治理设备,焊缝需要进行百分之百的无损检测,以确保设备的安全性和可靠性。
五、实际应用案例分析
(一)案例背景
某***型化工企业新建一套恶臭治理系统,其中包括多台废气处理设备和管道输送系统。由于处理的废气中含有多种腐蚀性成分,对设备的密封性和耐腐蚀性要求极高。为确保设备的质量和性能,该企业决定在设备制造过程中采用全自动焊接技术,并实施严格的工艺控制。
(二)全自动焊接技术应用
1. 设备选型
根据设备的结构***点和焊接要求,选用了适合的全自动焊接设备,如龙门式自动焊机、管道自动焊机等。这些设备具备高精度的控制系统和先进的焊接工艺,能够满足不同部件的焊接需求。
2. 焊接工艺实施
针对废气处理塔的筒体焊接,采用了埋弧自动焊工艺。通过***控制焊接电流、电压和焊接速度,保证了焊缝的成型质量和内部质量。对于管道系统的焊接,采用了氩弧焊打底、手工电弧焊填充盖面的复合焊接工艺。氩弧焊打底保证了焊缝的根部融合和密封性,手工电弧焊填充盖面则提高了焊接效率和外观质量。
(三)工艺控制措施
1. 焊接参数***化
根据设备的材质(不锈钢)和厚度,进行了详细的焊接工艺评定试验。通过试验确定了***的焊接电流、电压、焊接速度等参数,并在实际生产中严格按照这些参数进行焊接操作。同时,针对不同厚度的板材,调整了相应的参数补偿值,确保焊接质量的稳定性。
2. 焊前准备与预处理
在焊接前,对所有的材料进行了严格的表面处理。采用喷砂除锈的方法,将金属表面的油污、铁锈等杂质清除干净,使表面达到 Sa2.5 级清洁度标准。同时,对工件进行了***的装配和定位,使用了专用的夹具和定位块,保证了装配间隙和错边量在允许范围内。
3. 焊接过程监控与质量控制
在焊接过程中,安装了焊接参数监测系统和焊缝成型监控系统。实时监测焊接电流、电压、焊接速度等参数的变化,以及焊缝的余高、宽度等成型指标。一旦发现异常情况,立即停止焊接并进行调整。焊接完成后,对所有的焊缝进行了外观检查和无损检测。外观检查主要检查焊缝的表面成型、余高、宽度等是否符合要求;无损检测采用了超声波检测和射线检测相结合的方法,对焊缝内部质量进行全面检测。经过检测,所有焊缝均符合质量要求,一次合格率达到了[X]%以上。
(四)应用效果
通过采用全自动焊接技术和严格的工艺控制,该恶臭治理系统的设备制造质量和性能得到了显著提高。设备在运行过程中,密封性能******,没有出现任何气体泄漏现象。焊缝的耐腐蚀性也得到了有效保证,经过长时间的运行,没有发现明显的腐蚀迹象。同时,由于全自动焊接技术的高效性,设备的制造周期******缩短,为企业节省了时间和成本。该案例充分证明了全自动焊接技术和工艺控制在恶臭治理设备制造中的重要性和可行性。
六、结论
在恶臭治理***域,全自动焊接技术和工艺控制是确保设备质量和性能的关键因素。全自动焊接技术以其高精度、高效率、高稳定性的***势,取代了传统的手工焊接方式,为恶臭治理设备的制造提供了可靠的技术支持。而工艺控制则贯穿于焊接过程的始终,从焊接参数的***化选择、焊前准备与预处理到焊接过程的监控与质量控制,每一个环节都至关重要。通过合理的工艺控制,能够充分发挥全自动焊接技术的***势,保证焊接质量的稳定性和设备的可靠性。在实际工程应用中,应根据恶臭治理设备的具体***点和要求,选择合适的全自动焊接技术和工艺控制方法,并不断进行***化和完善,以提高恶臭治理系统的整体运行效果和经济效益,为环境保护事业做出更***的贡献。